Stainless steel machining
With the right tools and a good step-by-step plan, you can grind, brush or finish stainless steel to any desired result. We are happy to advise you!
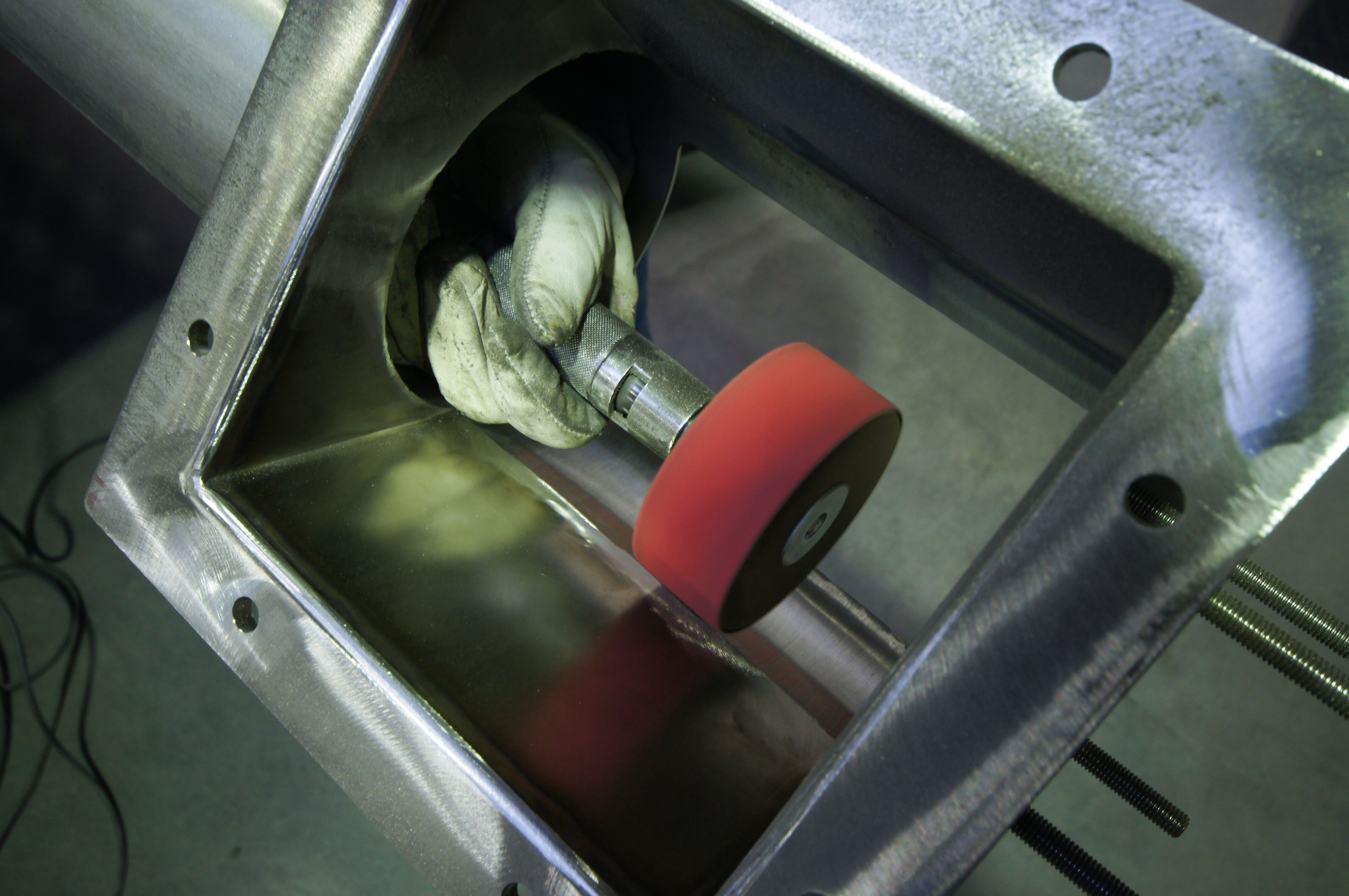
Working stainless steel, use the right tools
Stainless steel is a beautiful product that we encounter every day in various forms. It is important to choose the right abrasive for fast work. For fast material removal and tight work we recommend the 3M CubitronII fibre disc, especially for stainless steel. The best and most popular fibre disc in the market. Order directly in our webshop: 3M27618.
Or see here the other fibreglass discs in our product range
A commonly used product for processing stainless steel is Sctoch Brite. Read more about this versatile product on our special page.
Scotch Brite is a unique product made up of a web, resin and abrasive grain, and is available as an aggressive product for deburring, removing mill scale and finishing welds to applying a grinding structure. It does not affect the base material, making it very suitable for finishing.
Sheet metal stainless steel
We often find stainless steel in the form of sheet metal in tanks, boiler construction, interiors, machines and constructions. Particularly in the food and pharmaceutical industries, stainless steel is used a great deal because of its many favourable properties. Hygiene is an important example of this.
After all, in the food and pharmaceutical industries in particular, a low roughness of sometimes as much as 0.2 is a tough requirement from a hygiene point of view.
Stainless steel does not mean that stainless steel cannot rust, because this metal can. We call this corroding. Stainless steel is therefore not maintenance-free, but it is low-maintenance. A decisive factor in preventing corrosion is the availability of oxygen.
Stainless steel is covered with a protective oxide layer. This colourless and transparent layer protects the parent metal from corrosion. If this layer is damaged, the mother metal can corrode. Fortunately, this chromium oxide layer has a self-healing ability whereby oxygen is essential. That is why it is important to always keep stainless steel parts clean, so that dirt does not impede the access of oxygen.
Grinding stainless steel for roughness
The smoother the surface, the less dirt can adhere. Furthermore, a smooth surface is also easier to keep clean and to clean. These are important benefits when it comes to food and health. By choosing a stainless steel ground plate you can be sure that your material meets all requirements. By also specifying the Ra and Rz values you are assured of a stainless steel plate that meets all requirements over the entire surface. The difficulties begin when the sheet material is machined. Setting, cutting and certainly welding, always results in post-processing.
Many of our customers work in the stainless steel industry. Every day, we visit those companies on the shop floor to think along, suggest improvements and test. By working together in production, Metaaltechniek becomes an extension of your production. At the same time, we get a good insight into the wishes, but also the challenges that our customers face. These wishes and challenges are discussed weekly during the meetings of our field staff. In this way, we share knowledge, success stories, new insights, test results and we gain insight into the developments in the total market.
Remove inner corner weld on stainless steel with Rapid Cut
Removing an internal corner weld on stainless steel is a common operation. This is fast and easy with Rapid Cut discs from 3M. These discs contain the famous CubitronII grain which provides a fast material removal. The Scotch Brite web provides a nice finish, so you can quickly achieve.
Apply a brush structure to stainless steel
Brushing stainless steel is also called satin finishing. When brushing stainless steel, you apply an even scratch pattern, which visually gives a beautiful matt finish. This finish is often used for utensils in everyday life. Think of the extractor hood, banisters, vending machine casings, etc. All made of brushed stainless steel. The advantage of a brushed finish is that the product is less susceptible to scratches and if scratches do occur, they are less noticeable. Discolouration of the material is also easily removed with satin.
Use a stainless steel masking tape to get a nice tight mitre line.
Metaaltechniek provides a unique solution for satinizing: the PTL system. For faster changes and less risk of damage.
PTL stands for Push-Turn-Lock, a quick-change system as simple as it is unique, without a fastening bolt. This allows you to change wheels quickly without any additional mounting parts. You also have no annoying protruding fixing bolt, which means that you can work tightly along edges and in inside corners.
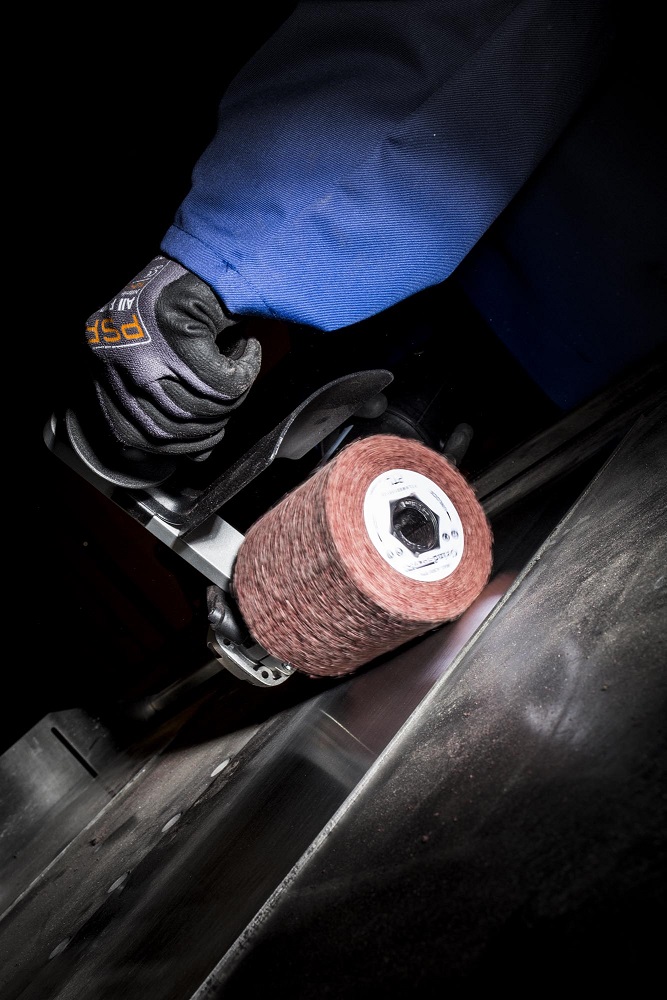
An innovation that makes changing between different finishing brushes a lot easier. The PTL range is continuously expanding. From brushes with only sanding cloth for quick stock removal to brushes with only Scotch Brite for finishing stainless steel plate and the combined brush. We also have a large assortment of polishing brushes. Go to our web shop to view and order the complete range of PTL.
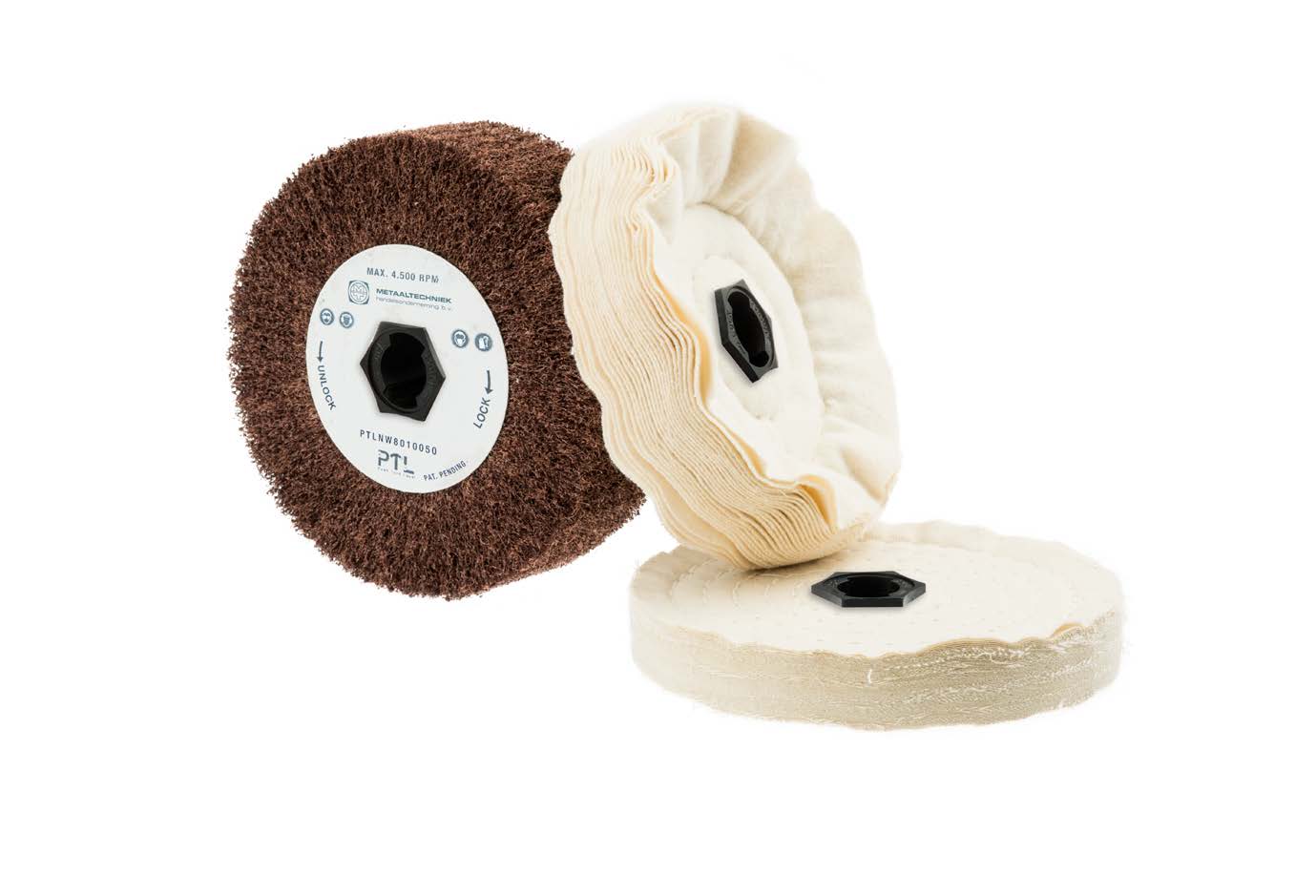
Applying a welding edge to stainless steel
Applying welding edges has many advantages. The main reason for applying welded edges is to make the welded construction more solid. The welding edge provides a larger welding surface, allowing the welding consumable material to adhere in more places. This improves the connection between the two sheet metal parts. At the same time, it also improves the through-welding, making the materials completely one.
- Enlarging the welding surface
- Improve weld throughput
- Reduce price
The application of welding edges reduces the cost price, because less welding consumables need to be used. In addition, the quality/price ratio of the workpiece improves. The quality improvement is greater than the costs required for the application of welding edges.
There are different ways to apply a welding edge. We'll figure out four ways:
- Apply the welding edge with an angle grinder combined with a deflashing disc. A method traditionally used in the heavier state and construction blue. Also in shipbuilding and offshore this is a popular combination because of its robustness and because it works reasonably fast. However, the disadvantage is the noise level and the vibrations. This is not only tiring for the operator but also ensures a less tight finish.
- Apply the welding edge with an angle grinder combined with a flap disc. This combination already works more quietly and gives a nicer finish because a lamella disc has some flexibility. At the same time, this flexibility ensures that the finish is not always tight.
- Apply the welding edge with an angle grinder combined with a fibre disc. In the vast majority of cases this is the best combination if you pay attention to speed and the quality of the finish. But also for the user this is a fine method because of the noise level and relatively little vibration.
- Apply the welding edge with a BevelMate combined with a tungsten carbide edge cutter. Especially a nice application if you work with a welding robot because of the constant finish.
Automatic deburring or grinding of stainless steel
Automatic grinding or deburring of stainless steel sheets, has a number of important advantages. Besides saving time, especially if you do a lot of serial work, the finish is always consistent and reproducible. Regardless of how the operator feels or how his weekend was. Also, working with an angle grinder is often perceived as dirty and not fun. When the same work is done by a machine, it is often perceived positively by staff and you work on bonding your people. Aluminum and steel are also suitable for automatic machining. We cooperate with Q-Fin because of the great Grinding Power of the Q-fin machines. We also offer all consumables, from sanding belts, bowl brushes and round brushes for all brands of deburring machines.
Radius or weld edge on stainless steel with Q-Fin and Beveltools
In cooperation with Beveltools, Q_Fin has developed a new table machine specifically for applying a weld edge or radius to stainless steel. The principle is based on Beveltools' hand machines, which work with a solid carbide milling cutter. The new geometry of the cutter, the stability of the head, the micro-lubrication, the whole new concept ensures a very constant machining and the lifetime of the cutter has increased by up to 300% compared to its predecessor. Watch the video and contact us for a demo!
Mirror plate polishing of stainless steel
Polishing to mirror plate is a time-consuming job and requires a lot of experience. Even after a day at METAC, our training center, you can't polish all at once. With the TopGrinder from Q-Fin it is a bit easier, though. Watch our video to get an impression of the possibilities.
Delve into the documentation
Improve your knowledge
Looking further
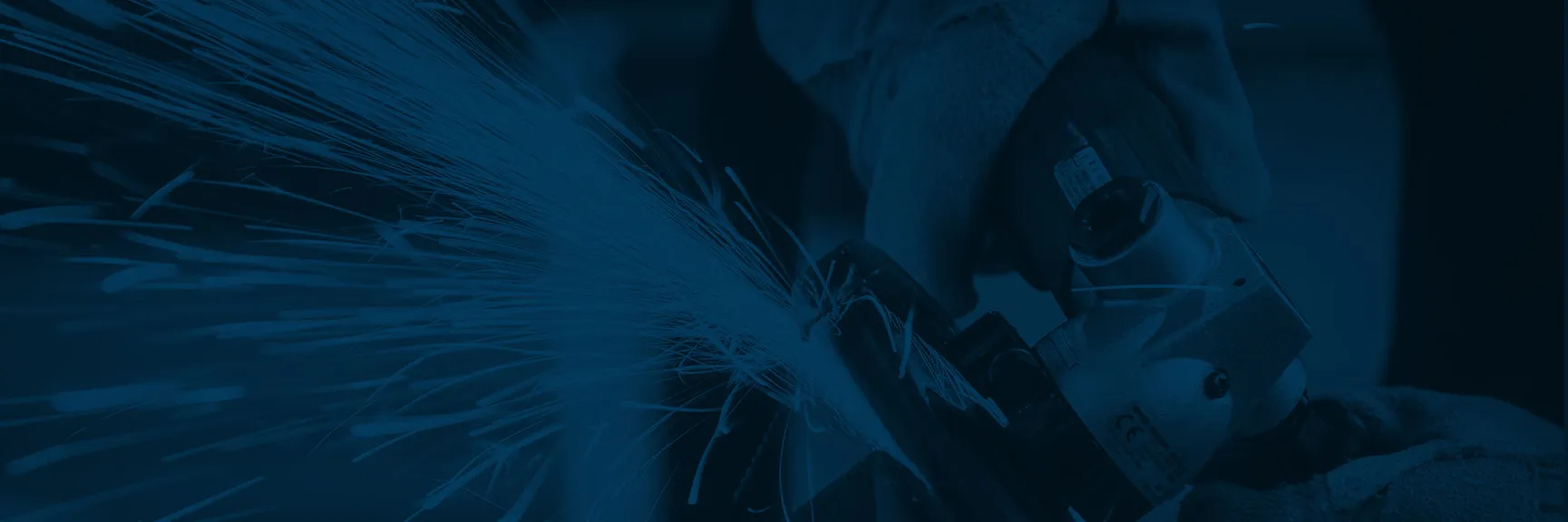