Grinding in offshore and heavy steel construction
Heavy steel constructions require tools made for heavy duty applications and the right combination of machine and machining product.
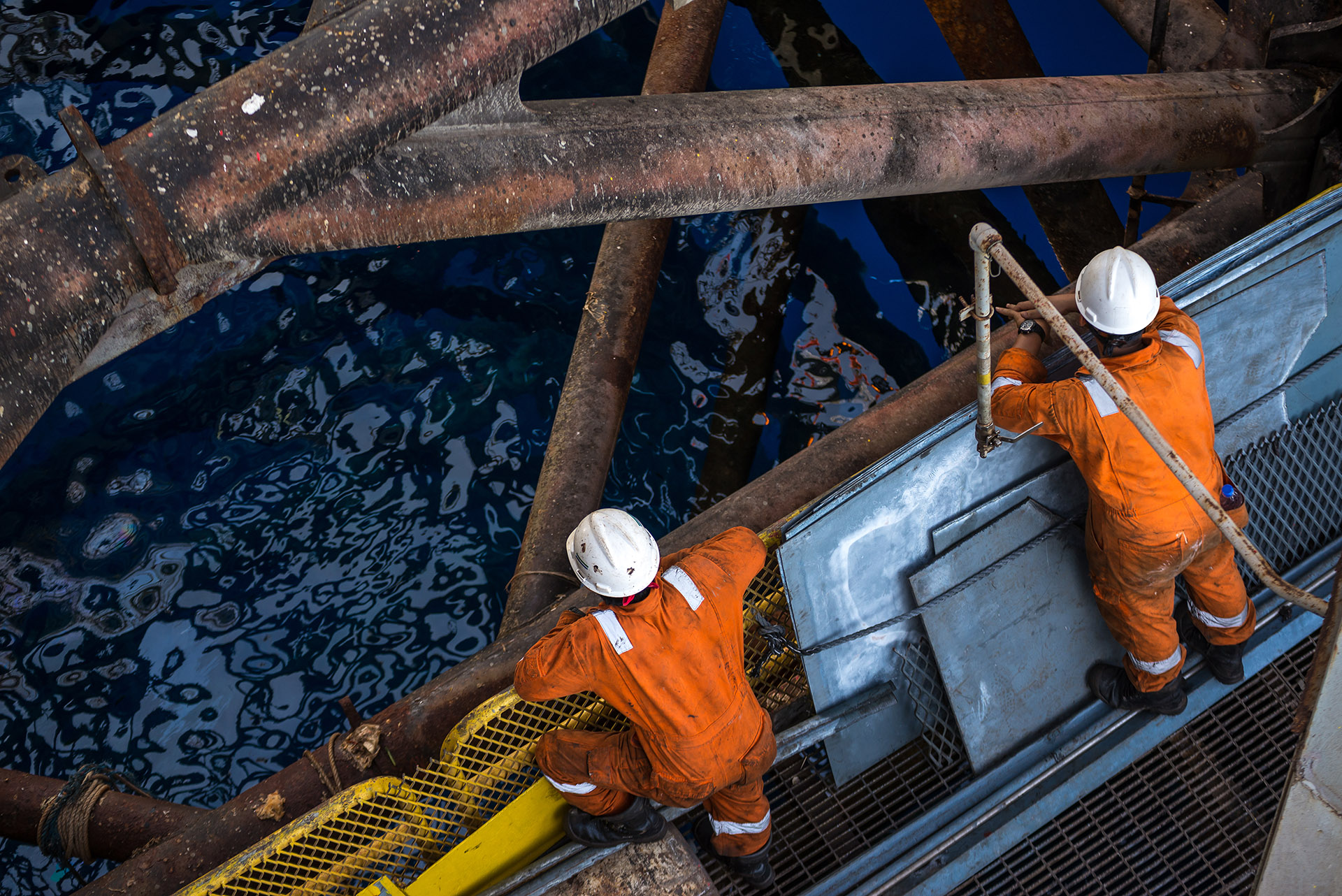
Grinding of steel to a radius of 2mm
In addition to the roughness of the surface, the finish of the sharp edges is also an important item. Usually a radius of 2 mm is sufficient, but a radius of 3 mm is already required for agricultural vehicles. In addition to the fact that sharp edges can cause dangerous cuts, it is also important for powder coating, for example, that a product has rounded edges. In order to adhere to material, powder coating does need surface. On sharp edges, the coating will retract. Also, paint on a rounded side is less susceptible to impact damage.
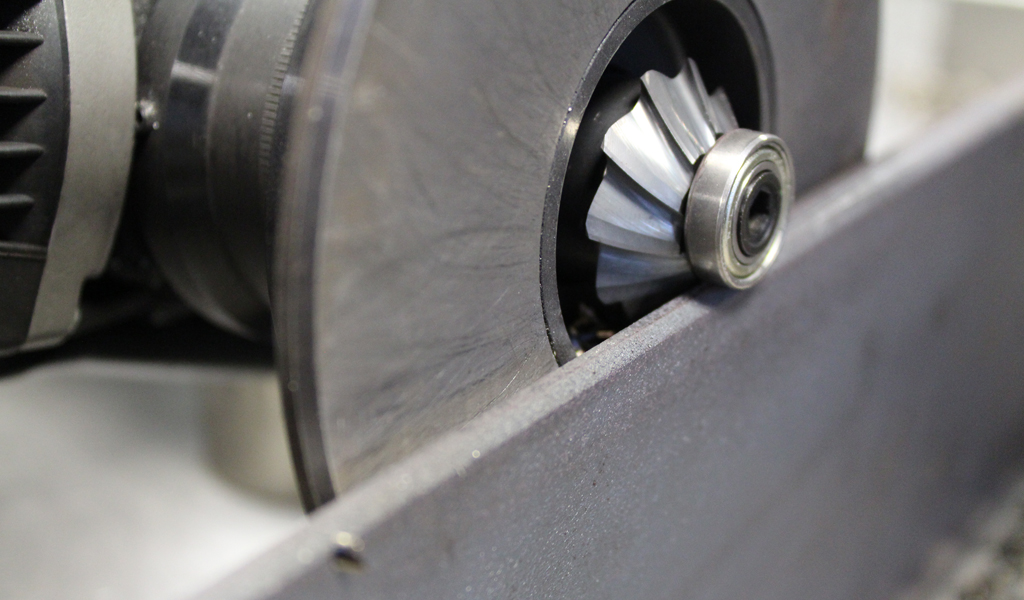
Different way of grinding steel on a 2 mm radius.
Here we mention three possibilities that specifically and accurately grind on an R=2, but there are surely more to come.
Rounding with a radius cutter using a hand-held machine:
Above you see a picture of the Bevel Mate machine by Beveltools. With a special radius cutter, you can apply a constant radius in one smooth motion. Due to the multitude of cutters in both sizes and angles, there is always a possibility to fill in your application. Click here for the possibilities in machines and cutters by Beveltools.
Automatic rounding with the Q-Fin SER600:
This deburring and grinding machine is equipped with 5 processing stations: a grinding unit (1st station) followed by 4 oscillating brushes (stations 2+3) and 2 round brushes (stations 4+5). You can use this machine to apply a large rounding (R2) to your metal cutting parts. The Super Edge Rounder is suitable for flat sheet metal parts from 4 to 40 mm thick and up to 600 mm wide. The ideal machine for finishing sheet metal parts that are to be powder coated or galvanised.
Semi-automatic rounding with the TopEdge from Q-Fin.
The TopEdge from Q-Fin is a manually operated machine with which you can easily and quickly mill various radii or weld edges at various angles. With the TopEdge you can apply a good weld edge or mill a radius (e.g. for good edge coverage in powder coating) inexpensively and with little effort. This enables you to produce according to all applicable guidelines. The TopEdge is equipped with an infinitely variable speed and a clamping table with hole pattern. Workpieces can be clamped onto the table; in combination with the 2-button control, you can always work safely. The balanced arm and sufficient mass of the milling head allow you to mill a constant and accurate radius or bevelled edge with little physical effort and vibration. The milling head is adjustable in various positions (angles) for various operations. In addition, the milling head is equipped with an adapter that makes it easy to change tools. Most of the milling heads available worldwide (e.g. those of Beveltools) can be used on the TopEdge. In addition, various adapters are available. The size of the work surface is 1200 x 780 mm. The maximum dimension for a workpiece is therefore 780 mm. The length is unlimited, as the side panels of the work table can easily be lowered.
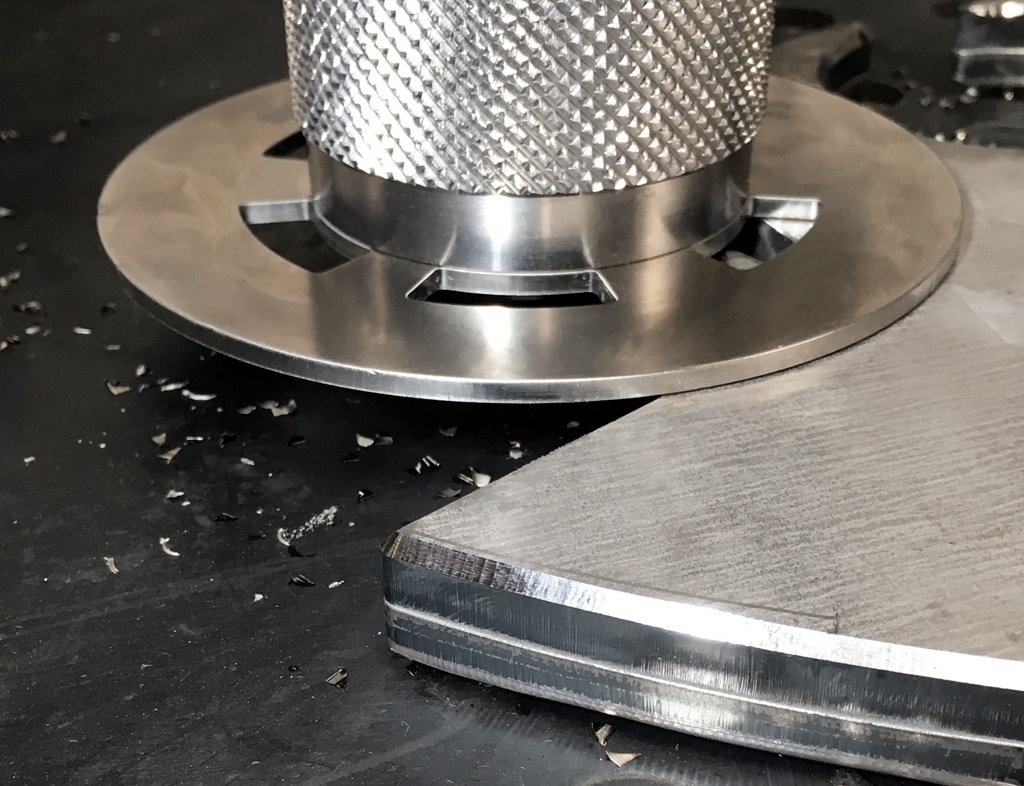
Applying a welding edge to steel
Applying welding edges has many advantages. The main reason for applying welded edges is to make the welded construction more solid. The welding edge provides a larger welding surface, allowing the welding consumable material to adhere in more places. This improves the connection between the two sheet metal parts. At the same time, it also improves the through-welding, making the materials completely one.
- Enlarging the welding surface
- Improve weld throughput
- Reduce price
The application of welding edges reduces the cost price, because less welding consumables need to be used. In addition, the quality/price ratio of the workpiece improves. The quality improvement is greater than the costs required for the application of welding edges.
There are different ways to apply a welding edge. We'll figure out four ways:
- Apply welding edge with an angle grinder combined with a deburring wheel.
A traditionally widely used method in the heavier state and construction breeze. It is also still a popular combination in shipbuilding and offshore because of its robustness and because it works reasonably quickly. The disadvantage, however, is the noise level and vibrations. This is not only tiring for the operator but also makes for a less tight finish. View our range of deflashing discs in the web shop.
- Applying the weld edgewith an angle grinder combined with a flap disc.
This combination already works more quietly and gives a nicer finish because a slat wheel has some flexibility. At the same time, that flexibility means that the finish is not always tight.
- Apply welding edge with an angle grinder combined with a fiber wheel.
Inthe vast majority of cases, this is the best combination if you consider speed and quality of finish. But this is also a fine method for the user because of the noise level and relatively little vibration.
- Applying bevel with a BevelMate combined with a carbide edge mill.
Especially a great application when working with a welding robot because of the constant finish.
Take a look at the video in which we review everything.
Delve into the documentation
Improve your knowledge
Looking further
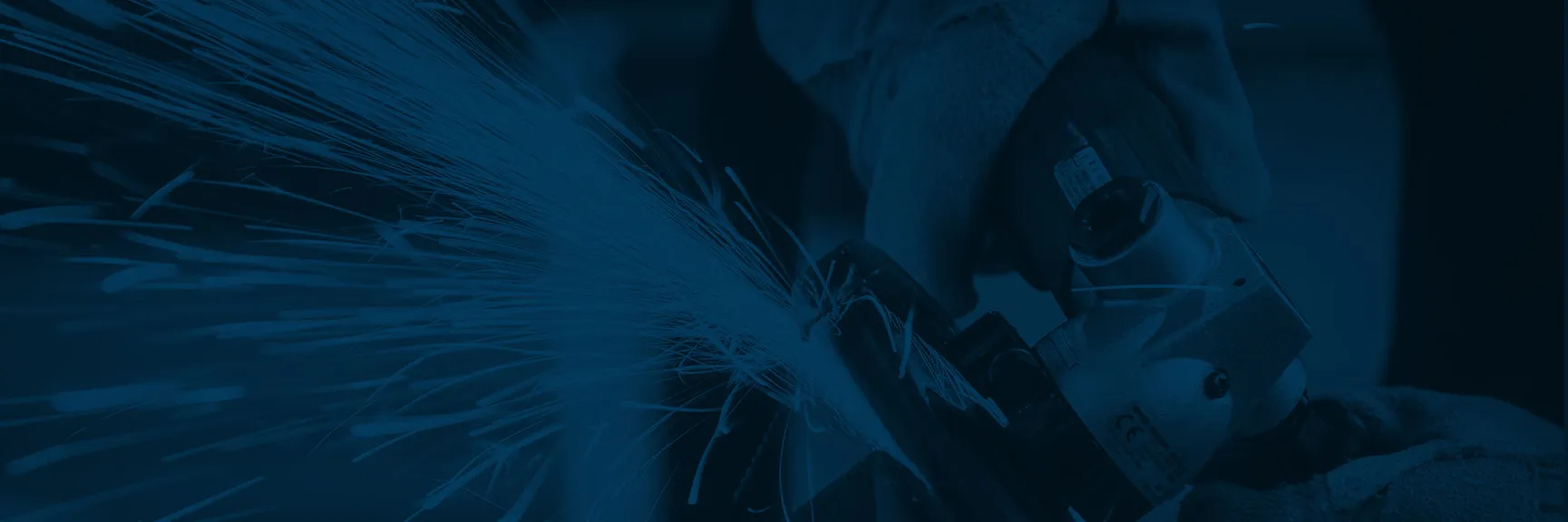